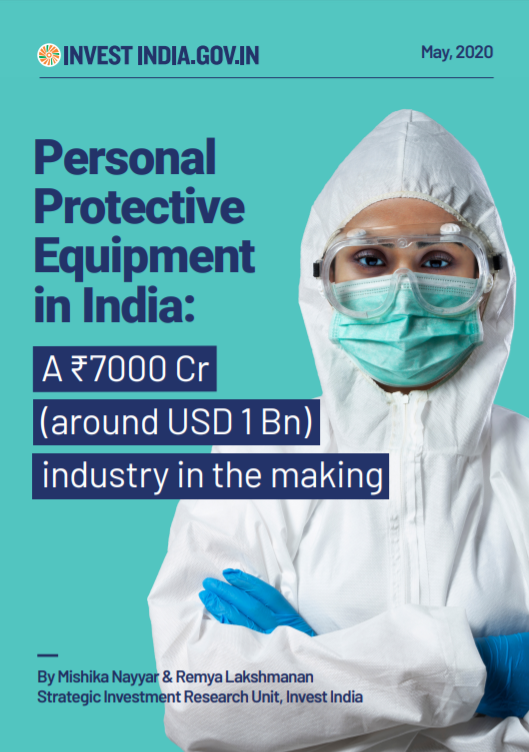
The COVID-19 pandemic is the defining global health crisis that the world is currently facing. The virus has spread all over the world, and the number of cases is rising every single day as governments work to slow its spread. The global response to the unfolding COVID-19 crisis saw countries implementing countrywide or partial lockdowns, the announcement of stimulus packages and relief measures to tackle the harsh economic impact of the pandemic. The virus also overwhelmed the global production capacity of PPE which is the most critical product to protect the front-line health workers and other responders. Surging demand for PPE kits along with disrupted global supply chain amid the Covid-19 pandemic was putting lives at risk.
India moved quickly, implementing a nationwide lockdown with the goal of flattening the curve and using the time to plan resource responses, adequately. The Prime Minister assured the country that there are ample reserves of medicines, PPE kits, food and other essential goods.
India realized the critical role of PPE in combating this pandemic as early as March, wherein the Ministry of Textiles stepped to lead the assessment of the availability of all protective wears for our frontline health workers.
What followed this, is a remarkable journey of collaboration between governments at the central and state levels, industries and workers to revamp existing production lines to manufacture a completely unknown product, from scratch.
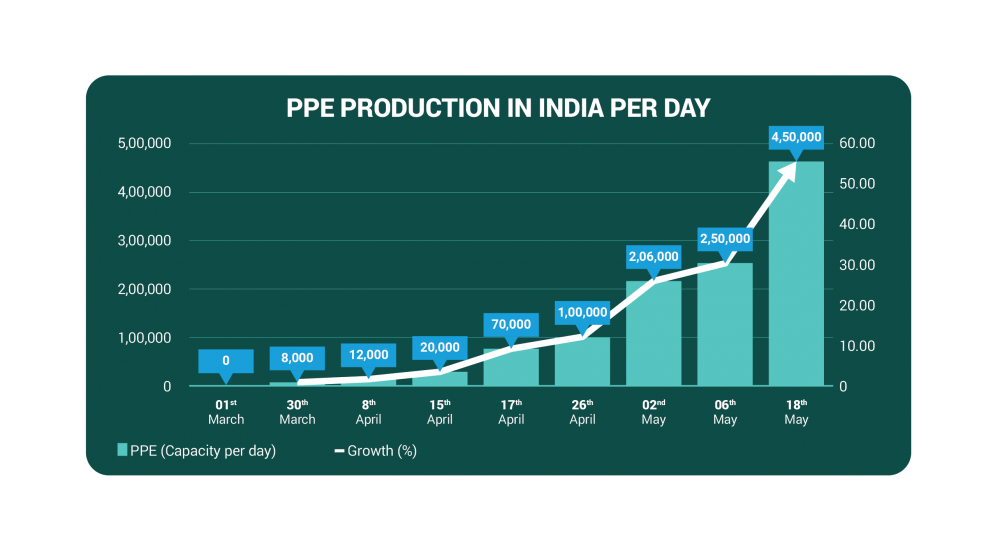
- From 0, India now produces nearly 4.5 lakh PPE kits every single day.
- In 60 days, the PPE industry in India has witnessed 56 times growth.
This is a testimony to the government of India’s concerted efforts of improving domestic manufacturing capacity on the back of its industrious manufacturing sector at such challenging times. Before we proceed further, we must understand what PPE exactly is.
What is Personal Protective Equipment (PPE)?
Personal Protective Equipment (PPEs) are protective gears designed to safeguard the health of workers by minimizing the exposure to a biological agent. PPEs include goggles, face-shield, masks (Surgical/N-95), gloves (surgical/examination), coverall/gowns (with or without aprons), head cover and shoe cover.
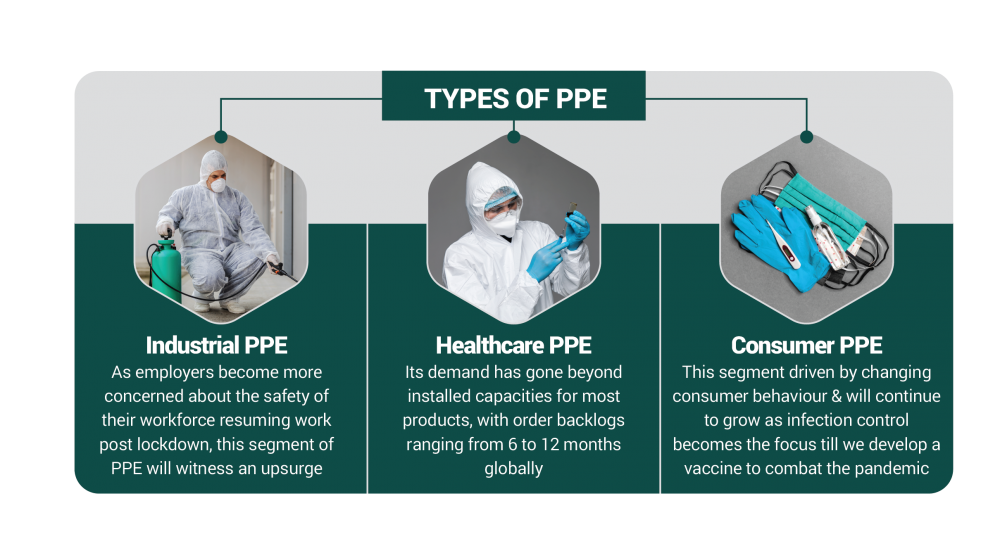
The Ministry of Health and Family Welfare released a set of guidelines for the rational use of PPE for health care workers and for others who work at various point of entries, quarantine centres, hospitals, laboratories, primary healthcare and community settings.
The guidelines emphasize the need to select the right type of PPE based on the estimated risk of contamination, the reuse of PPEs when there is a shortage and, the procedures to be followed on how to wear them.
More details in Annexure 1.
Several stakeholders played a crucial role in ramping up the production of critical products
Role of Ministry of Textiles in enabling India become a world leader in PPE manufacturing
On March 1, two days before the World Health Organization (WHO) spoke of a global shortage of PPE, India had no PPE coveralls suitable for Covid-19. India was a complete import dependent as far as PPE kits are concerned. In January, there were only 275,000 PPE kits available, owing to timely import.
On March 18, 2020, Ravi Capoor, Secretary, Ministry of Textiles chaired a joint meeting of officials and industry representatives to assess the availability of protective wears for use by health professionals. Major shortages of PPE were being reported across the country, posing much danger for frontline workers who tend to COVID-19 patients. An import dependent India then charted a journey to become not only self-sufficient but a world leader in PPE manufacturing.
An outreach programme was launched by Ministry of Textiles and Ministry of Health & Family welfare (MoHFW) in this regard, inviting fabric and garment manufacturers to develop suitable product and build manufacturing capacities on war-time basis.
Several round of meetings, discussions and active collaboration with Indian technical textiles industry had been initiated to meet the 7.25 Lakh requirement as projected by MoHFW on March 18, until June. The projected demand has again been revised to 1.5 crore in 1st week of April and is currently projected at 2 crore until July 2020.
Between 2nd to 25th February 2020, a number of test samples of fabrics developed by Indian medical textiles manufacturers were sent to The South India Textile Research Association (SITRA), the centre of excellence for medical textiles for testing. The test results conducted on the various fabric samples were shared with MoHFW immediately which finalised the technical specification on March 2, 2020 based on WHO’s interim guidelines for protective equipment for COVID-19.
On March 23, 2020, the very first day of the nationwide lockdown had the Ministry of Textiles gearing up to fight COVID-19 using a multi-pronged strategy. Under the able leadership from the Minister of Textiles and Secretary, Ministry of Textiles, an Emergency Control Room was set up to monitor production and supply of medical textiles (N-95 mask, body coveralls and meltblown fabric) which are required in connection with COVID-19.
Emergency control office was to work 24*7 and was placed under the supervision of P K Kataria, Special Secretary and the following officers were made in-charge: Nihar Ranjan Dash, Joint Secretary, H K Nanda, Director, Balram Kumar, Director, Pankaj Kumar Singh, Dy. Secretary, Padmapani Bora, Dy. Secretary.
To take stock of the situation from ground level, the Ministry of Textiles also involved the Office of the Textile Commissioner in Mumbai, Central Silk Board in Bengaluru and Textile Committee based in Mumbai and placed the following officers in-charge from respective bodies: Molay Chandan Chakravarthy, Ranjit Ranjan Okhandiar and Ajit B Chavan.
Several industry players who offered their existing facilities to manufacture PPE, received immediate guidance and assistance from the Ministry of Textiles. While facilitating the activity of trade in the middle of a nationwide lockdown, the emergency control room coordinated efforts with several state governments and ensured the supply chains of all raw materials including fabric, zippers, tapes, requisite machinery were maintained 24*7. From collection of samples from different parts of the country to transporting them to SITRA, Coimbatore through Lifeline Udaan service of Ministry of Civil Aviation, the government provided all possible facilitation measure for indigenous development of PPE manufacturers.
“We faced humongous challenges of non-availability of domestic manufacturers of repute and incessant delay/long gestation period to import machines from China. We therefore decided to do it indigenously,” said Ajit Chavan, secretary, Textiles Committee and Additional Textile Commissioner, Ministry of Textiles.
While the Ministry of Textiles took charge of maintaining the supply of PPE, the Hindustan Latex Limited (HLL) was made the centralised handling agency for medical procurement to streamline the demand of PPE. Later, apart from SITRA, the Defence Research and Development Organisation (DRDO) was added as another testing and certifying agency to help speed up the manufacturing process. In order to maintain quality of high standards, it has been made mandatory to obtain Unique Certification Code (UCC) for each tested sample, prior to supply; and emboss the details of UCC, name of manufacturer, date of manufacturing/batch number etc. on each PPE.
The Ministry of Health and Family Welfare (MoHFW) released a set of guidelines for the rational use of PPE for health care workers and for others who work at various point of entries, quarantine centres, hospitals, laboratories, primary healthcare and community settings. The guidelines emphasize the need to select the right type of PPE based on the estimated risk of contamination, the reuse of PPEs when there is a shortage and, the procedures to be followed on how to wear them.
More details in Annexure 1.
The Ministry of Textiles continues to conduct market regulations and due diligence by taking stringent actions on suppliers/manufacturers whose proto-type samples for PPE have failed laboratory tests but are still reaching the market. The first detailed note on quality control protocol for PPE was released by the Ministry of Textiles on April 6, 2020 followed by its periodic revisions on April 22, 2020 and May 5, 2020.
A clear roadmap and prompt assistance by the Ministry of Textiles and all its allied bodies, ensured India becomes a world leader in PPE manufacturing amid a global shortage. At present, India has 10 laboratories approved for testing and certification of PPE coveralls for COVID-19.
More details in Annexure 2.
India is the World's 2nd Largest PPE Manufacturer in the World in Just 60 Days
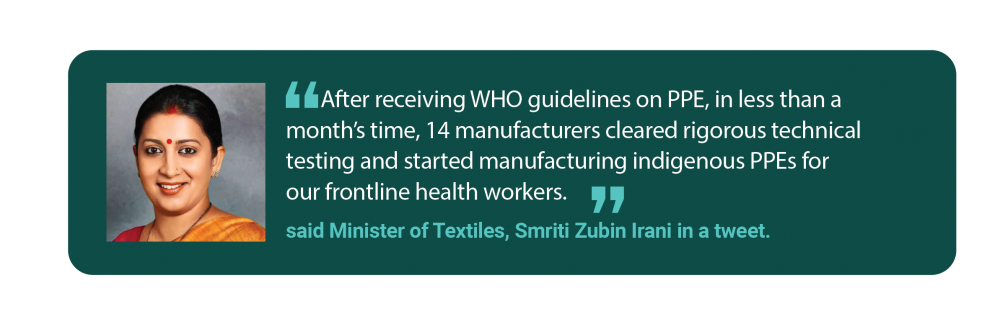
The situation has now undertaken an unprecedented turn wherein, as of date, India has about 15.96 lakh PPE kits in the centre-state buffer stock and orders for another 2.22 crore PPE kits have already been placed to domestic manufacturers.
Currently, India has about 15.96 lakh PPE kits in the centre-state buffer stock and orders for another 2.22 crore PPE kits have already been placed to domestic manufacturers.
Geographically, Bengaluru, Karnataka has become a major hub for PPE coverall production in the country accounting for nearly 50 per cent production. Besides Bengaluru, PPE coveralls are also being manufactured by approved production units in Tiruppur, Chennai and Coimbatore in Tamil Nadu, Ahmedabad and Vadodara in Gujarat, Phagwara and Ludhiana in Punjab, Kusumnagar and Bhiwandi in Maharashtra, Dungarpur in Rajasthan, Kolkata, Delhi, Noida, Gurugram and few other places.
The Indian textile manufacturing industry came to the fore in this exercise, where they initially began with manufacturing of masks followed by complete PPE sets, including body coveralls, gloves, shoe covers, etc. The textile sector is gearing up to start producing these goods, which comes under the medical textiles segment, with a view to making India a hub for sourcing of PPE kits over the next few years.
Production of PPE is proving to be a commercially viable product category and a saviour in this time of crisis wherein economic uncertainties loom large owing to the effects of the nationwide lockdown.
Now, the domestic production of PPE in India is being currently pegged at about 4.5 lakh PPE kits per day. This mammoth growth has been achieved owing to domestic manufacturers who rose to the occasion and helped India attain a self-sufficient status in the production of PPE.
Until 31st May 2020, total production of PPE Body Coveralls from indigenous sources has crossed 1.1 Crore. (Read here)
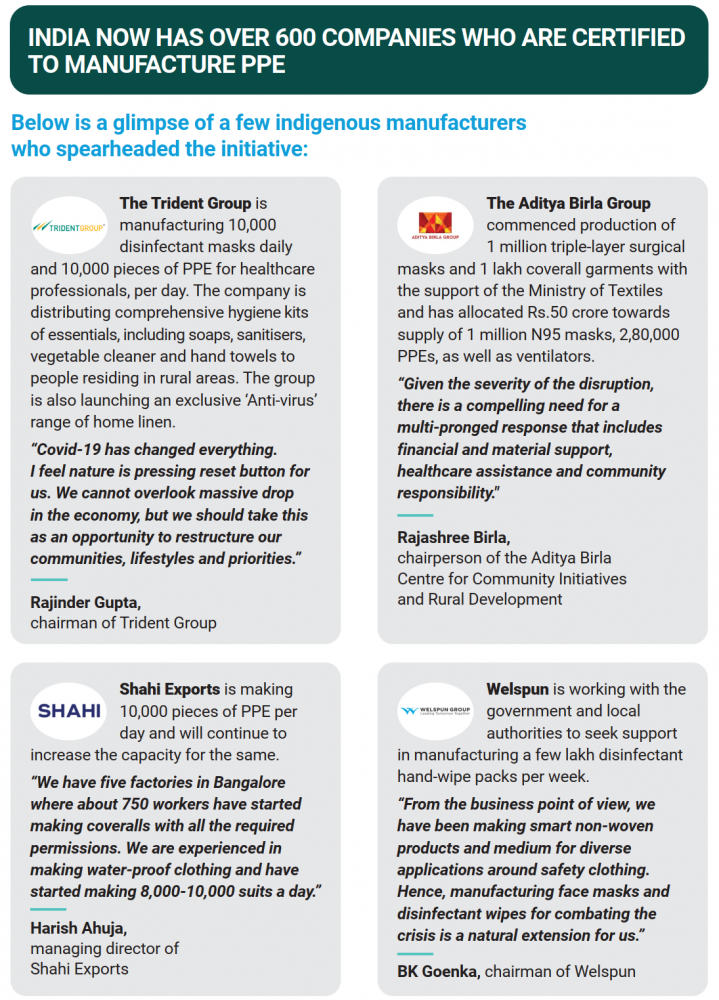
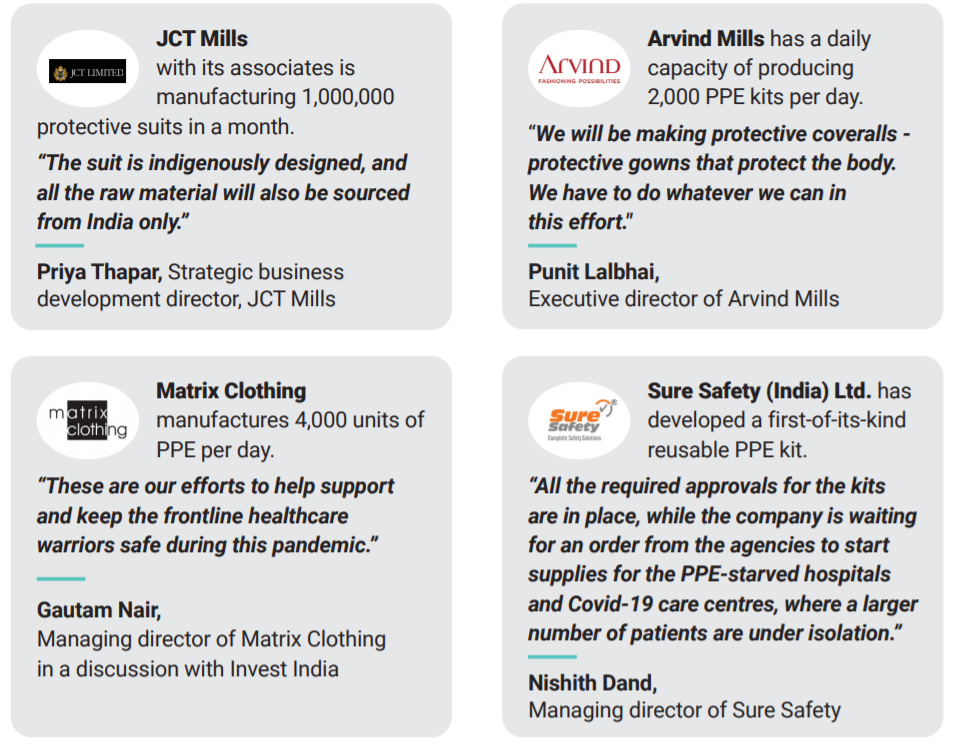
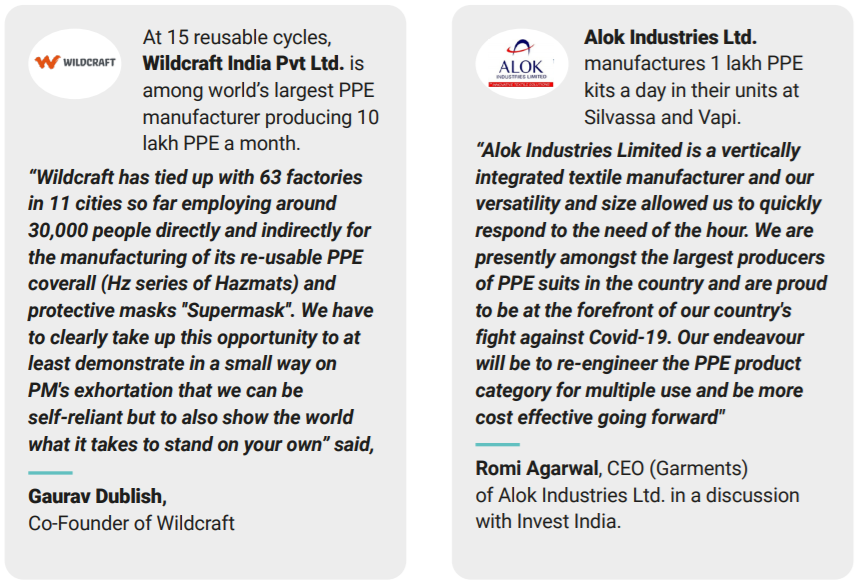
A cluster-based approach to manufacturing PPE: Tiruppur
South India’s cotton knitwear capital, Tiruppur, has geared itself to step up production as demand for PPE has brought to the fore, an INR 15,000 crore worth business opportunity this fiscal year. The garment cluster manufactures textiles worth INR 60,000 crore a year for exports and domestic markets. About 200 units currently make PPE, mostly to serve needs within India. The local industry body, Tiruppur Exporters Association, has been pushing these units to improvise on products to meet global standards to make PPE manufactured in India more export-oriented, in conjunction with the rising global demand. The Association estimates this to be an INR 10,000-15,000 crore revenue opportunity, this year alone.
"According to a study, there will be domestic demand of PPE worth INR10,000 crore for the next one year and internationally there will be a $60 billion business in 2025, whereas India has done only $260 million so far last year."
- A. Sakthivel, Chairman of Apparel Export Promotion Council (AEPC) in a webinar organised by AEPC on PPE manufacturing under medical textiles
Further, he added that though many of the PPE products needed for frontline health workers are banned for exports currently, but once the local manufacturers meet the Indian demand, they should be allowed to export. AEPC has already submitted a request for this to the government. Sakthivel further notified that AEPC will have a separate cell for PPE, as its immediate task is to provide sufficient kits domestically to prevent their further imports.
"We have a vibrant Indian and global market. Please reach out to doctors who are near you and understand these medical professionals who will wear these PPE. Connect with them and understand the practical aspects of breathability, wearability issues that they are having and create garments for that. If you are able to satisfy that customer then the world is at our feet.”
- K. S. Sundararaman, Chairman of Indian Technical Textiles Association (ITTA) in a webinar organised by AEPC on PPE manufacturing under medical textiles
“We have two classifications – single use and reusable. Both are widely acceptable in today’s scenario because disposal of single use is becoming very complicated. So, reusables are also slowly coming in.”
- Prakash Vasudevan, Director, South Indian Textile Research Association (SITRA) said in a webinar organised by Apparel Export Promotion Council (AEPC) on PPE manufacturing under Medical Textiles.
Efficient response and farsightedness of the Indian Railways & Indian Navy: An exemplary testimony of public commitment
The World’s 4th Largest Railway Network, to Manufacture PPE
The pandemic also saw the Indian Railways, a treasured public utility system that came to a standstill due to the lockdown, quickly convert its resources to start in-house production of PPE kits as a mission. The entire production by Jagadhari workshop in Yamunanagar district of Haryana was cleared by DRDO and over 17 workshops are committed to this exercise.
With the specification for the PPE kits, the resources and the material suppliers in place, over 6 lakh masks were produced as of 9th April and the mission aims to continue producing minimum three sets per sewing machine per hour to meet 50% of the PPE requirements of the country.
Duly contributing its bit in the fight against COVID-19, the Indian Navy is ready to help the industry to mass PPE kits. A team formed by the Innovation Cell, Institute of Naval Medicine, Mumbai along with the Naval Dockyard, Mumbai collaborated to design and produce PPEs.
Tested and approved by the Institute of Nuclear Medicine and Allied Sciences (INMAS), which is a laboratory of the DRDO, the PPE is noteworthy for the innovative choice of fabric used, which gives the PPE its 'breathability' and ‘penetration resistance’ rendering it both comfortable and safe for the user.
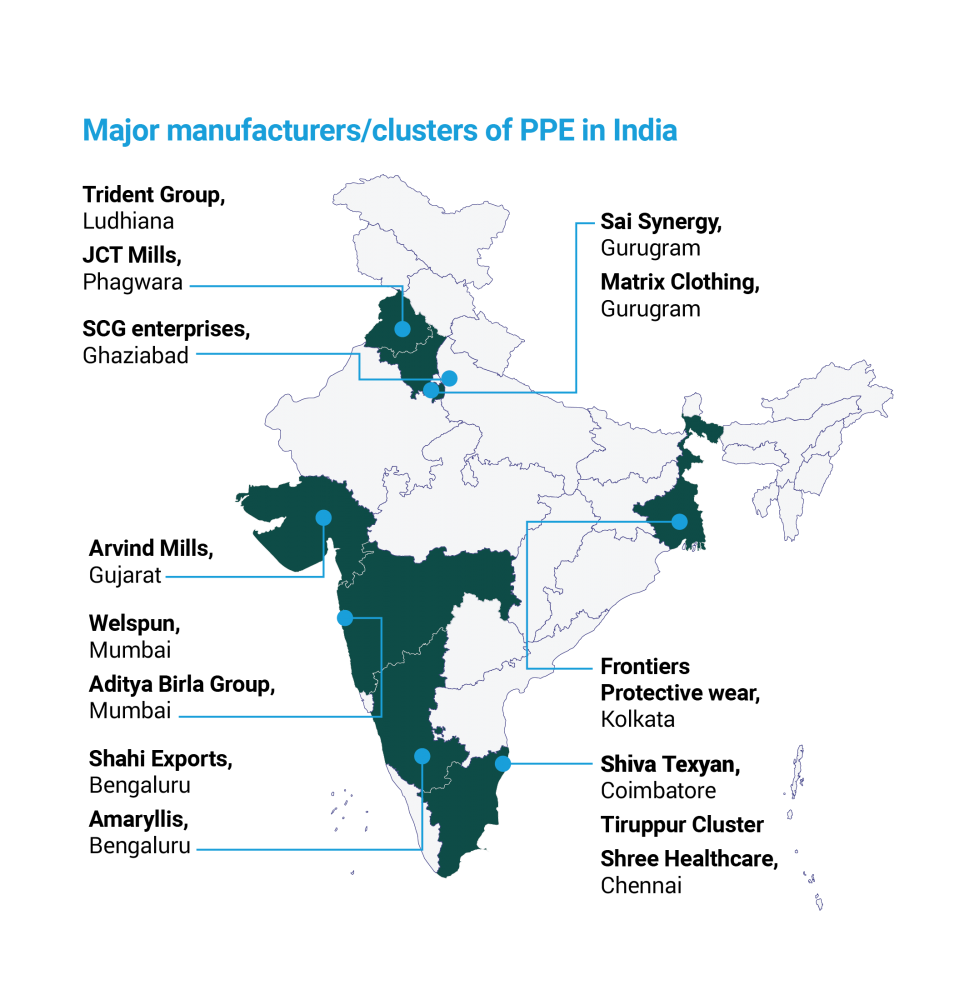
Tapping into the Global Demand
As industry insights suggest, most of them see PPE as a long-term product category going ahead, as these products will be more in demand across the globe in future.
The World Health Organization (WHO) has estimated the requirement for 89 million medical masks each month along with 76 million examination gloves and 1.6 million medical goggles.
“Healthcare workers rely on PPE to protect themselves and their patients from being infected and infecting others. Without secure supply chains, the risk to healthcare workers around the world is real. Industry and governments must act quickly to boost supply, ease export restrictions and put measures in place to stop speculation and hoarding. We can’t stop COVID-19 without protecting health workers first.”
- Dr Tedros Adhanom Ghebreyesus, WHO Director-General
To meet the rising global demand, WHO estimates that the industry must increase manufacturing capacity by 40%.
Governments should develop incentives for industry to ramp up production by easing restrictions on the export and distribution of personal protective equipment and other medical supplies.
The spread of Covid-19 has sky-rocketed the global demand for PPE and China, being the largest producer of PPE kits affected in the initial stages of the outbreak, has led to massive disruption of the global supply chain. Most countries in Europe and North America rely on Asia for 60% to 70% of their PPE supply. Besides China, Taiwan alone makes up for 20% of the supply of face masks, while other countries with PPE production capacity, include India, Japan, Korea, Malaysia, Mexico, Thailand, United States (US), and several European countries.
The industry is a mix of big and small players but largely dominated by established manufacturers like 3M, Ansell, DuPont. Honeywell Safety Products, Kimberly Clarke Corporation, Lakeland, Moldex-Metric and others, who are rising to the occasion to meet the global demand.
The global PPE market was valued at $52.7 billion in 2019 and is expected to reach $92.5 billion by 2025, growing at a CAGR of 8.7% during 2020-2025.
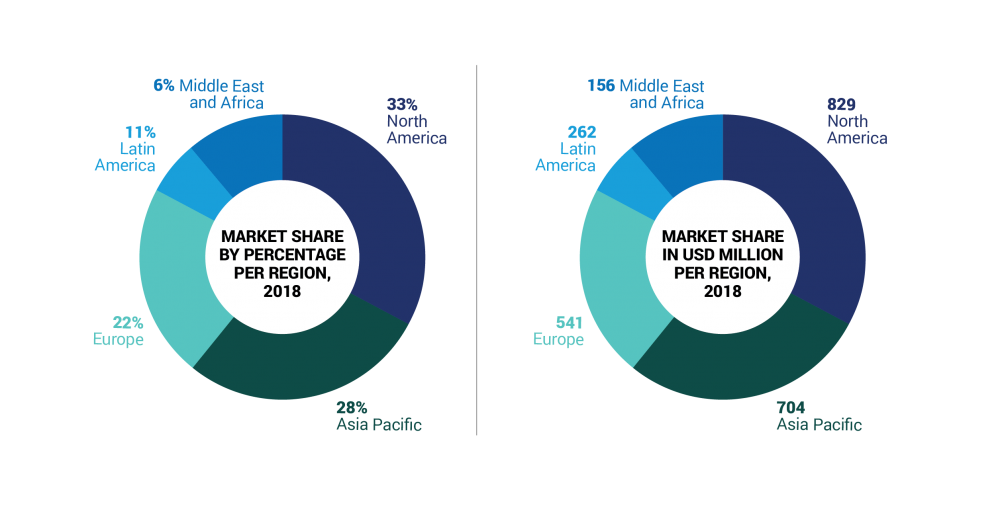
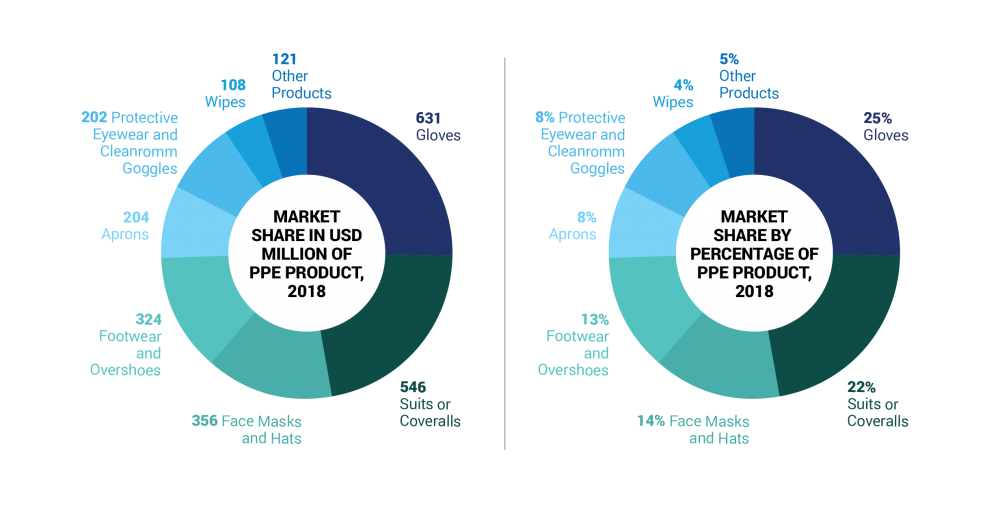
The Road Ahead
As the virus ravaged even the most developed countries of the world, India has shown its superior leadership, solidarity and its mind for innovation and quick thinking. India, achieving an unrealistic goal of producing 4.5 lakh of PPE kits within three months of the virus outbreak, exemplifies its abilities, resources and commitment to its people. Over the years, India has exhibited strong links to the global community, assisting countries on several occasions in the past. India should rise to this moment and going forward, be even better primed to meet the expectations and demands of its global family
Some key points to address some of the bottlenecks, and strengthen the supply distribution of PPE in both domestic and cross-border trade:
- Strengthen local supply chains - Given the potential for border closures or unanticipated delays in procuring raw materials from other states, governments both at the central as well as the state levels, must be proactive in planning to localize, regionalize and secure shorter supply lines. Government initiatives such as reducing the cost for licensing facilities and products, expediting development of high-speed manufacturing lines and other strategies to assist companies in overcoming barriers to new production, will encourage local companies to be able to shift production to making PPE equipment.
- Opening borders - Post Covid-19 crisis, the Indian government must re-evaluate current bilateral and multilateral trade agreements and envision new ones that enable supplies of critical components and materials. India is one among the top countries in Asia with maximum number of Free Trade Agreements (FTAs), either in operation or under negotiation or proposed. Overall, with the exception of a few agreements like South Asian Free Trade Area (SAFTA), India has been unable to fully leverage most of its FTAs. Hence, it is important that India implements the necessary measures to remove these obstacles such as high cost compliance and strict regulation that hinder the overall competitiveness of exports in the country.
- Tie up with technology companies – As one of the largest technology providers, India can leverage the technical know-how and build analytics to create efficient PPE supply chain management mechanisms to monitor high demand of critical products. This will enable to predict surges in ordering, maintain optimum stock levels, limit wastage and avoid stock-outs. PPE forecasts, based on rational quantification models, can ensure the rationalization of requested supplies; assist in monitoring and controlling PPE requests from countries as well as large responders and promote a centralized request management approach.
- Global standards to improvise indigenous PPE products – This will prove to be a benefit in the long-term to make PPE manufactured in India, more export-oriented in conjunction with the rising global demand. Gathering data by capturing ratings and reviews of PPEs and developing universal fit guidelines, will also help manufacturers focus on wearability while keeping in mind their safety and efficacy. Disposing and processing of PPE suits is damaging to the environment and with sustainability becoming increasingly important to companies, reusable PPE gears will be preferred and will see a spike in demand in the future.
- Strengthen supply chain and optimally utilize trade finance programs for Micro, Small, and Medium-sized enterprises (MSMEs) – MSMEs are particularly vulnerable to the economic and trade impact of COVID-19. Many and most of the PPE supply manufacturers in India are also MSMEs, who may be experiencing supply chain disruptions, and due to reduced sales and trade, facing liquidity and working capital constraints. Trade finance programs for MSMEs by multilateral organizations such as World Bank and the Asian Development Bank can help facilitate domestic and global trade by financing MSMEs in developing economies like India.
- Leveraging India’s vibrant research and development ecosystem – For greater growth and competitiveness through enhanced innovation to improve the efficacy of PPE, it is imperative that India seeks collaboration with countries who are lead innovators in this segment alongside bolstering up the research institutions. Knowledge transfer at an international level can be achieved through research partnerships, building strategic alliances with countries with whom India already has a track record of collaborative research and exploring such research in the form of virtual institutes.
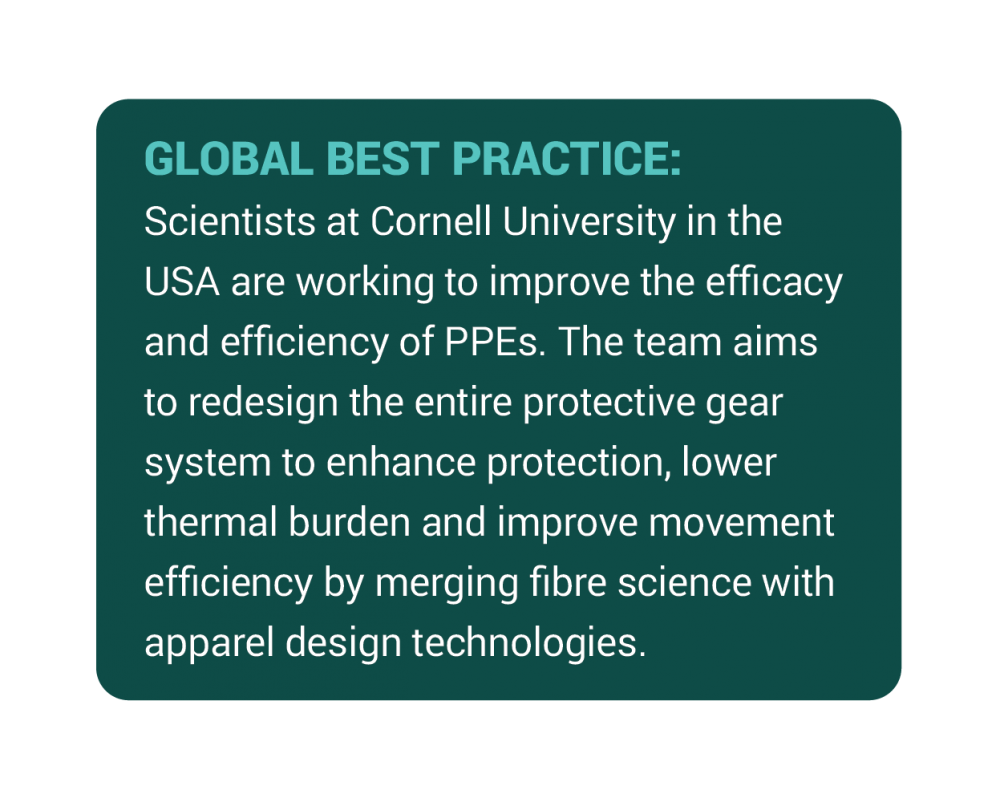
Annexure 1
Following are the steps taken by Government of India to procure, increase manufacturing and ensure safe distribution of PPE suits crucial in fight against COVID-19:
- Additional guidelines on rational use of Personal Protective Equipment (setting approach for Health functionaries working in non-COVID areas)
Click to read the notification
Date: 1 May 2020 - Guidelines on rational use of Personal Protective Equipment
Click to read the notification
Date: 1 May 2020 - SITRA approved list of Fabric Manufacturers for Coveralls (2 releases)
Click to read notification 1
Click to read notification 2
Date: 24 April 2020 - Quality Control Mechanism for PPE Body Coveralls Manufactured in India
Click to read the notification
Date: 22 April 2020 - List of Fabric Manufacturers for making PPE body coveralls approved by SITRA
Click to read the notification
Date: 15 April 2020 - Two laboratories under OFB equipped with Blood Penetration Resistance Test Facilities for Testing Body Coveralls for COVID-19
Click to read the notification
Date: 11 April 2020 - Exemption from BCD and Health Cess on import-Ventilators, PPE, COVID Test Kits and Face, Surgical Masks
Click to read the notification
Date: 9 April 2020 - A total of 2.94 lakh PPE coveralls have been arranged and supplied by Government of India. Negotiations are in final stages with a Chinese platform for placing an order of 60 lakh complete PPE kits
Click to read the notification
Date: 6 April 2020 - Manufactures / Suppliers whose proto-type samples for Body Coveralls for COVID-19 have failed Laboratory Tests, are still supplying their PPE in Market
Click to read the notification
Date: 6 April 2020 - PPEs are being procured from the central pool and distributed to all the States across the country
Click to read the notification
Date: 6 April 2020 - Production capacity of coveralls required by medical personnel treating COVID-19 cases in the country has been ramped up to more than 1 lakh per day
Click to read the notification
Date: 6 April 2020 - Minutes of the 12th meeting of Technical Textiles for Medtech Applications Sectional Committee
Click to read the notification
Date: 3 April 2020 - Personal protection equipment (PPE) kits are used by medical personnel working in isolation areas and intensive care units to protect them from acquiring infections. They were not being manufactured in the country. With the prospect of huge requirement of PPEs arising in the near future, the Government of India made proactive efforts to promote their manufacturing in the country.
Click to read the notification
Date: 30 March 2020 - The Ministry of Textiles has set up an Emergency Control Room to monitor production and supply of medical textiles (N-95 mask, Body Coveralls and meltblown fabric) which are required in connection with Covid-19.
Click to read the notification
Date: 25 March 2020 - Emergency control Office in the Ministry of Textiles for monitoring and facilitating supply of PPE and other materials for Covid-19
Click to read the notification
Date: 24 March 2020 - Minutes of meeting with MOT to assess the availability of protective wears for use of health professional in country in the wake oF COVID-19
Click to read the notification
Date: 18 March 2020
Annexure 2
S. No. | Name | Contact Details | Address | Website Link |
1 | The South India Textile Research Association (SITRA), Coimbatore, Tamil Nadu |
Mr Suresh Ram, Phone No.: 07530035499 Email: sitrameditech@sitra.org.in |
Centre of Excellence for Medical Textile The South India Textile Research Association 13/37, Avinashi Road, Coimbatore, Aerodrome Post Coimbatore, Tamil Nadu 641014 |
Link |
2 | Institute of Nuclear Medicine and Allied Sciences (INMAS) DRDO, Delhi |
Brig. S. K. Mazumdar Phone No.: 011-23905170/ 23905105/ 23905105 E-mail: director@inmas.drdo.in |
Rajaji Marg, Vijay Chowk Area, Central Secretariat, New Delhi, Delhi 110004 |
|
3 | Heavy Vehicles Factory, Avadi, Tamil Nadu |
Mr Sanjeev Kishore, Sr. General Phone No.: 044-26843000; E-mail: hvf.ofb@nic.in |
Heavy Vehicles Factory, Avadi, Chennai, Tamil Nadu 600054 | Link |
4 | Small Arms Factory, Kanpur, Uttar Pradesh |
Mr A. K. Maurya, General Manager; Landline No: 0512-2295042/46 E-mail: saf.ofb@nic.in |
Small Arms Factory, Kalpi Road, Kanpur, Uttar Pradesh 208009 | Link |
5 | Ordnance Factory, Muradnagar, Uttar Pradesh |
Mr D. K. Meena, Works Manager; Phone No.: 9462696751; E-mail: ofm.ofb@nic.in |
Ordnance Factory Muradnagar, Ghaziabad, Uttar Pradesh 201206 |
Link |
6 | Ordnance Factory, Kanpur, Uttar Pradesh |
Mr A. N. Srivastava, General Phone No.: 0512-2295161-68/ 70; E-mail: ofc.ofb@nic.in |
Ordnance Factory Kanpur, Kalpi Road, Kanpur, Uttar Pradesh 208009 | Link |
7 | Ordnance Factory, Ambernath, Maharashtra |
Mr Santosh Kumar Sinha, General Manager; Phone No.: 0251- 2610211, 2613132, 2613660, 2613750; E-mail: ofa.ofb@nic.in |
Ordnance Factory Ambernath, Ambarnath, Thane, Maharashtra 421502 |
Link |
8 | Metal and Steel Factory, Ishapore, West Bengal |
Mr Sanjay Chawla, General Manager; Phone No.: 03325938400; E-mail: msf.ofb@nic.in |
Metal and Steel Factory, Ishapore PO-Nawabgunj-Ichhapur Dist - 24 Parganas (North), West Bengal 743144 | Link |
9 | Textiles Committee (TC), Mumbai Textile Laboratory & Research Centre |
Shri Kartikay Dhanda Phone: 91-22 66527 519/520/625 Fax: 91-22 66527 554 E-mail:dlab.tc@nic.in / tcppetest@gmail.com |
P. Balu Road, Prabhadevi Chowk, Prabhadevi, Mumbai-400025 | Link |
10 | NITRA (North India Textiles Research Association), Ghaziabad |
Phone:0120-2807390-95, 0120-2783586/592/638/095 Fax: 0120-2783596 E-mail: mail@nitratextile.org |
Sector-23, Raj Nagar, Ghaziabad-201002 | Link |
- https://www.tribuneindia.com/news/ludhiana/trident-to-make-10k-ppe-kits-daily-69908
- https://indianexpress.com/article/coronavirus/in-indias-fight-against-covid-19-a-made-in-punjab-hazmat-armour-6336884/
- https://www.thehindubusinessline.com/companies/vadodaras-sure-safety-develops-reusable-ppe-kits/article31415413.ece#
- https://economictimes.indiatimes.com/news/politics-and-nation/tiruppur-units-eye-2-billion-opportunity-from-ppe-biz/articleshow/75259440
- https://english.lokmat.com/national/apparel-exporters-gear-up-to-make-india-a-hub-for-sourcing-ppe-kits/
- https://www.business-standard.com/article/pti-stories/rising-demand-for-ppe-products-provides-huge-opportunity-for-domestic-exporters-
- https://www.who.int/news-room/detail/03-03-2020-shortage-of-personal-protective-equipment-endangering-health-workers-worldwide
- https://www.adb.org/sites/default/files/publication/579121/ppe-covid-19-supply-chains-bottlenecks-policy.pdf
- https://www.technicaltextile.net/news/cornell-university-team-improving-ppe-266410.html
- https://swarajyamag.com/insta/india-becomes-worlds-2nd-largest-ppe-kit-producer-in-just-two-months-develops-world-first-reusable-ppe-suit
- https://pib.gov.in/PressReleseDetailm.aspx?PRID=1612464
- https://www.unicef.org/supply/stories/covid-19-impact-assessment-and-outlook-personal-protective-equipment
- https://pib.gov.in/PressReleseDetailm.aspx?PRID=1621903#.XrRXvgH4-VY.twitter
- https://www.thehindubusinessline.com/news/aditya-birla-group-commits-rs-500-crore-to-combat-covid-19/article31249473.ece
- https://health.economictimes.indiatimes.com/news/medical-devices/india-ramps-up-production-of-covid-19-protective-gears-medical-